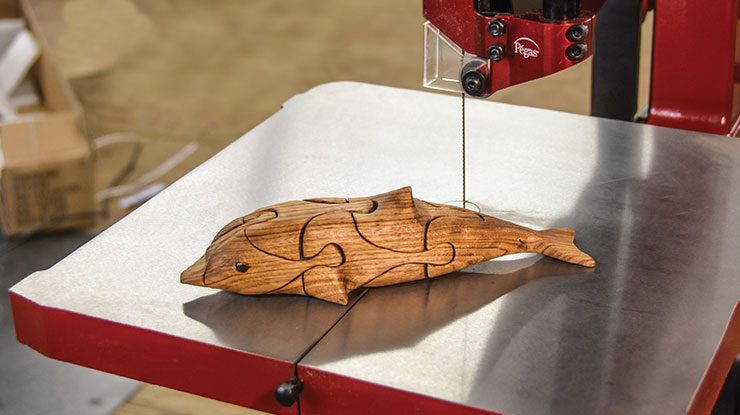
This guide is for those who are interested in intarsia-wood art. The following information covers Wood types, patterns, tools and techniques. Learn more about this fun craft. You might want to try different wood types depending on your skill level. Start by making a sample of this craft piece if it's your first time.
Patterns
Woodworkers who are skilled can make many intarsia projects including holiday, tree and flower ornaments. The book's intarsia wood pattern pages are suitable for all levels of experience and demonstrate the artistic nature of the process. 21 full-size Intarsia Patterns are included. There is also helpful information regarding shaping, wood and blades.
Intarsia allows you to create an original piece of furniture, or wall hangings by using different wood species. It is like building a puzzle with various pieces of wood placed next to one another. The wood is then polished or stained, and each piece is assembled to create a unique design that adds depth and character to the finished project. You will be able to make intarsia wooden patterns, but they can be very difficult to make.
Tools
You need to have special tools for intarsia. A small belt sander is an excellent tool for removing material quickly and smoothing the edges. A dremel, or flex shaft, can be useful if you are looking for a tool to shape and sand fine details. You can use these tools to create small areas or shape them with different tools.
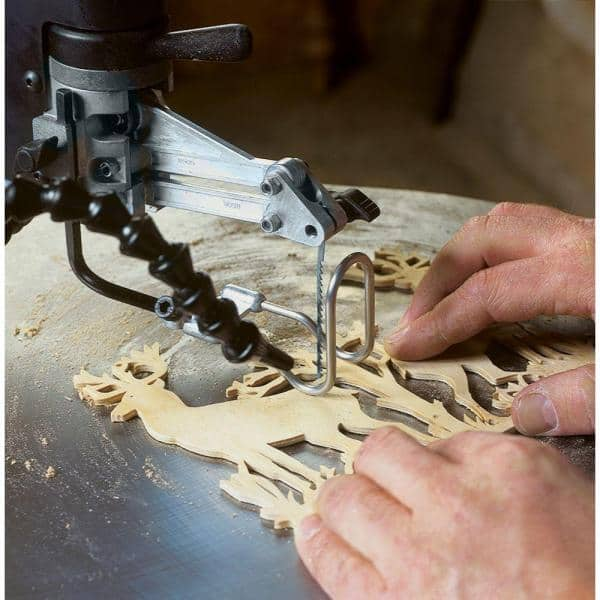
Jigsaws: Jigsaws work well for cutting wood but are not able to make intricate cuts like a scrollsaw. Sanders are also needed to smoothen out wood surfaces. Intarsia woodworking requires two different types of wood that contrast in color and grain. The wood can then be stained in a variety of ways. The wood will then be cut and sanded in order to create a mosaic design.
Techniques
You don't have to be a pro at intarsia. It is possible to create beautiful pieces of art if you know the right techniques. A pattern is a great starting point for your artistic creativity. With these ideas, you'll be well on your way to creating a stunning piece of intarsia wood art. Here are some methods:
Select the project design first. Keep extra copies of your template. Next, choose the species of wood you're going to use. Different wood species are different. Your project will have a deeper and more interesting dimension if you rough out the thickness of each wood piece. You can also add pieces to your project by gluing extra layers of wood. Finalize your project by removing all backing and leaving the finished intarsia.
Woods for your use
The new book provides the tools and techniques you need to make unique inlaid pieces. With Kathy's progressive approach to teaching, you'll learn about everything from the basics to the nuances of color breaks. Even if you've never made intarsia before, you'll find yourself referencing this book again as you learn more about this fascinating craft.
First, choose woods that complement one another and have the same grain orientation. For example, a teddy requires 20 pieces of wood that are made from four types of wood with slightly different grains. A saw with a high speed blade is required. Once you've figured out the wood's color and grain orientation, you're ready to move on to cutting and staining.
Colors
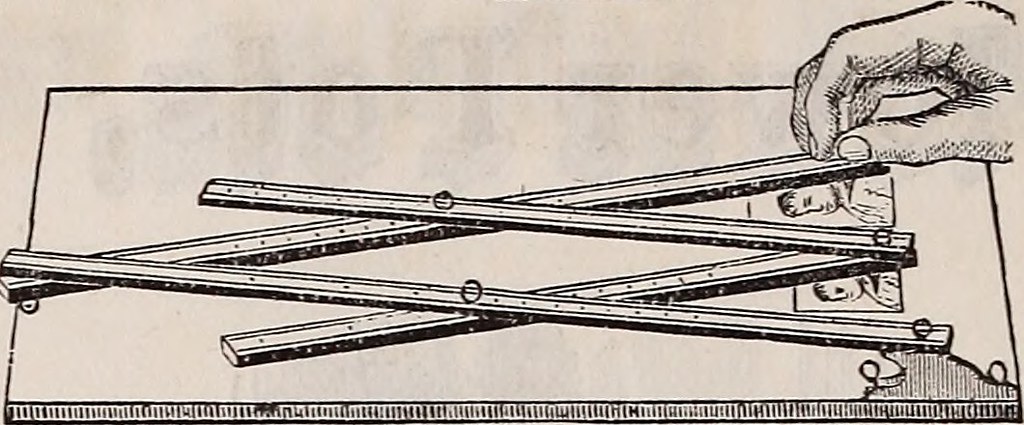
Intarsia is as diverse as the wood itself. While saps and heartwoods are either reddish brown or grey black, they are both white. Some woods darken with age, like cherry. Cherry's initial tone is light, but it becomes medium-colored when exposed in the sun. Cedar and other woods like it have varying tones. This adds depth to your project.
Intarsia refers to a type art made by joining different pieces of wood together and creating patterns. It originated in the Islamic world, but today is often associated with Italy. To create a three-dimensional effect, woodworkers use a variety of wood shades with different thicknesses. Intarsia colors are commonly found on jewelry boxes and wooden chests.
Time-consuming process
The intarsia process is a complex one, involving the use of different types of wood and staining techniques. Intarsia artists need to have different types of wood and different stains in order create beautiful patterns. Although plywood and Birch are the most popular types of wood, other types of wood are suitable. The type of wood that an artist chooses is entirely dependent on his or her personal preference. Intarsia projects can be created by many craftsmen using Western Red Cedar.
The first step of intarsia woodenworking is to cut the inlay and label it. The artist then glues or adheres the pieces. The glue is dried and the woodworker finishes it with a double bevel-inlay. This time-consuming process requires a great deal of skill, and the finished product is truly a work of art.
FAQ
What is the hourly rate for a woodworker?
The hourly rate for a professional woodworker varies depending on many factors, including skill level, experience, availability, location, and other variables.
A skilled woodworker can expect an hourly rate of $20-50.
A less skilled woodworker can charge as low at $10 an hour.
How can I determine which tools are most suitable for me?
It's important that you consider your needs and preferences while shopping for tools. Do you prefer metal or plastic handles? What size screws and nails do you use most often? Are you comfortable with power tools, or would you rather use hand tools?
Is it hard to start my own woodworking business?
It can be difficult to start your woodworking business. There are many requirements and regulations that must be followed. It doesn't mean that you have to go through the entire process of starting a business. Many people prefer to join existing companies. This will allow you to avoid paying membership fees and taxes.
Statistics
- The best-paid 10 percent make $76,000, while the lowest-paid 10 percent make $34,000. (zippia.com)
- Woodworkers on the lower end of that spectrum, the bottom 10% to be exact, make roughly $24,000 a year, while the top 10% makes $108,000. (zippia.com)
- The U.S. Bureau of Labor Statistics (BLS) estimates that the number of jobs for woodworkers will decline by 4% between 2019 and 2029. (indeed.com)
- Average lumber prices rose about 600 percent between April 2020 and May 2021. (familyhandyman.com)
External Links
How To
How to join wood without using nails
Woodworking is a hobby that many people enjoy doing. It is relaxing and enjoyable because you can create something useful with wood. There are times when two pieces of wood need to be joined together. This article will teach you how to do this to keep your woodwork projects looking great.
First, remove any sharp edges from the wood pieces before you join them. You don't want to leave sharp corners that could cause problems later on down the road. Now it's time to start glueing your boards together.
When working with hardwood, glue should be applied only to one side. If you're using softwoods like pine or cedar, you should put glue on both sides. Press the boards down until the glue is fully incorporated. After applying the glue, let dry the boards before proceeding to the next stage.
After you've glued your boards, you'll want to drill holes into the joints where you plan to insert screws. Depending on what type screw you choose, the size of these holes will depend on how big they are. For example, if you're going to use a 1/2-inch wood screw, then you should drill a hole that is at least 3/4 inches deep.
Once you've drilled your holes, you'll want to drive the screws through the joint and into the backside of the board. You should be careful not to touch the board's front surface. This could cause damage. When driving the screws, try to avoid hitting the ends of the screws too much. This will avoid splitting in the wood's ends grain.
Now that your project is finished, you'll want to protect it from the elements. You can seal the furniture pieces or cover the top. You will want to choose a product that will be durable for many years. Examples include oil-based varnishes and polyurethanes, shellac, lacquer and others.
These products are available at most home improvement stores. Just make sure that you buy the right kind for the job. Also, remember that some finishes are toxic and should never be used indoors. When handling certain finishes, wear protective gear.