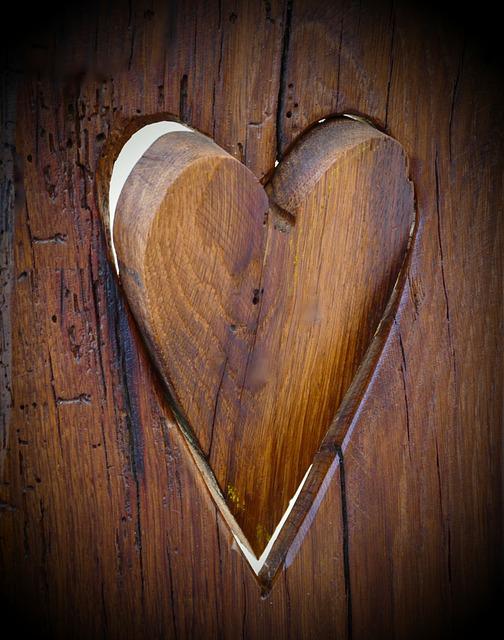
Before you begin carving your walking stick, it is essential to learn which woods work best. You will also want to know about various techniques for whittling and what David Allen uses to carve his walking sticks. A few famous quotes about walking sticks are also available. These are some tips to help you create the perfect walking stick. Keep reading to learn more. You can now carve a walkingstick that will be functional and unique!
Woods that can be used to carve a walking stick
Finding a straight blank is the hardest part of the whole process. While you may find some trees that have branches too long to be useful, you should continue searching until you find the right piece. You should harvest straight branches in the winter, when sap travels between the branches and roots. This makes the wood less likely to split and more stable. If you don't have the time to wait for spring, you can still harvest the wood while it is still green.
There are many wood species that can be used to make a walking sticks. The North American hardwood Chestnut is strong. Its density makes it ideal for making walking sticks and other similar tools. This species' wood grain is either slightly open or partially closed. It is a solid walking stick, which feels smooth and solid. It's also very attractive and widely used for carving. Some species can be carved with the bark left in place.
Techniques to whittle a walking sticks
There are a few basic techniques to carve a walking stick. First, pick a piece that has a unique texture. Some woods have distinct bark patterns and colors while other woods have natural twists. You may want to enhance these features by using lacquer or paint. To make it look more appealing, you could also carve the wood shaft. Make sure that the stick you choose is straight, free of branch shoots or hard spikes.
This book will explain the differences between different types of wood as well as different carving styles. The most commonly used designs are snakes, lions, and other savage animals. Not only can you carve snakes but fish, eagles, and even deer. These artists are often regarded as God-given. This is a book for the novice or the advanced carver.
David Allen uses these tools when carving a walkingstick
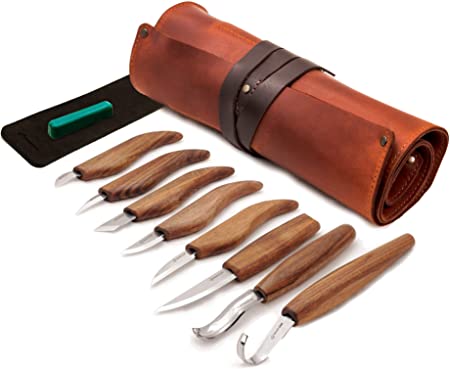
David Allen began to make toys as a child with a pocketknife that he found under his home. Because he was too young for a knife to be used, he had the knife hidden from his family. His creations included toys, like slingshots, as well as utilitarian tools like shoeshine cases. At the age of 15, Allen became disabled and began carving walking sticks. Allen used a pocketknife and chisel to carve out the wood.
Allen created his designs by himself, digging around sapling roots and then deciding what to carve. Allen believed that design must be "seeable" before carving can begin. This process was similar to that of many African-American artists. Allen had many visions and dreams of the design he wanted. Through this, he was capable of creating a stick that would inspire the emotions and feelings within his community.
Famous quotes about walking sticks
Carving a walk stick is a difficult process. You need a good blank. The most difficult part is to find a straight blank. Although there are many sources of your stick, it is important to persevere in finding one that is straight. It may appear bent beyond practical use, but keep searching until you find one. If possible, try to cut your stick during the winter when sap is flowing from the tree's branches to the root. Sap makes wood more flexible and less likely to break.
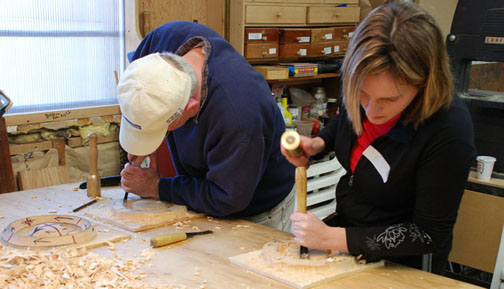
Consider the wood's texture when choosing wood. Every piece has a unique texture and color. There may be unique bark marks or swirls. A coat of lacquer will enhance these natural swirls. A smooth finish is possible by choosing a wood shaft that is free from branch shoots and tough spikes. This will make it easier. It doesn't matter what material or finish you choose, but it is worth considering the type of finishing that you will use.
FAQ
What material would you recommend to start learning woodworking?
You can start with softwoods like pine or poplar. After you are comfortable with the softwoods, move to hardwood.
You can learn how to woodwork.
It is best to do it yourself. Woodworking requires patience, practice and skill. Every craft takes practice and patience.
It is the best way to learn to do something is to actually do it. So start small and build on what you have learned from there.
Is it hard to start my own woodworking business?
It's not easy to start your own woodworking business. You will need to adhere to many legal requirements. But, this doesn't mean you need to go through all of the trouble of setting up your business. Many people decide to join established businesses. This allows you to join existing businesses and pay only membership fees.
Statistics
- Woodworkers on the lower end of that spectrum, the bottom 10% to be exact, make roughly $24,000 a year, while the top 10% makes $108,000. (zippia.com)
- Most woodworkers agree that lumber moisture needs to be under 10% for building furniture. (woodandshop.com)
- If your lumber isn't as dry as you would like when you purchase it (over 22% in Glen Huey's opinion…probably over 10-15% in my opinion), then it's a good idea to let it acclimate to your workshop for a couple of weeks. (woodandshop.com)
- In 2014, there were just over 237,000 jobs for all woodworkers, with other wood product manufacturing employing 23 percent; wood kitchen cabinets and countertop manufacturing employing 21 percent. (theartcareerproject.com)
External Links
How To
How to join wooden boards without using nails
Woodworking is a popular hobby. You can make useful items from wood with your hands, which is both relaxing and fun. However, there are times when you want to join two pieces of wood together without having to use nails. This article will explain how to do this so that your woodwork projects stay beautiful.
Before you can join the wood pieces together, you need to remove any rough edges. Do not leave any sharp corners as they could cause problems down in the future. Once you have done that, you can begin gluing your boards together.
If you're working with hardwood, you should only apply glue to one side. You should glue both sides if you are working with softwoods such as pine and cedar. After applying the glue, press the boards firmly until they are completely stuck together. Before moving onto the next step, make sure the glue has dried completely.
After you've glued your boards, you'll want to drill holes into the joints where you plan to insert screws. Depending on what type screw you choose, the size of these holes will depend on how big they are. For example, if your screw is a 1/2-inch wooden screw, drill a hole that is at minimum 3/4 inches deep.
Once you have drilled the holes, the next step is to drive your screws through the joint into the board's backside. Be careful not to hit the front surface of the board, or else you'll ruin the finish. Avoid hitting the screws' ends too often when driving screws. This will prevent splitting the wood's end grain.
After your project is completed, you will need to protect it from the weather. You have two options: seal the whole furniture piece or just the top. You want it to last years, so you can use any product. You can choose from oil-based varnishes or polyurethane, shellac and lacquer as examples.
These products can generally be found in any home improvement shop. You should make sure you are getting the right type for the job. Some finishes are toxic and should not ever be used indoors. Always wear protective gear when handling any of these finishes.