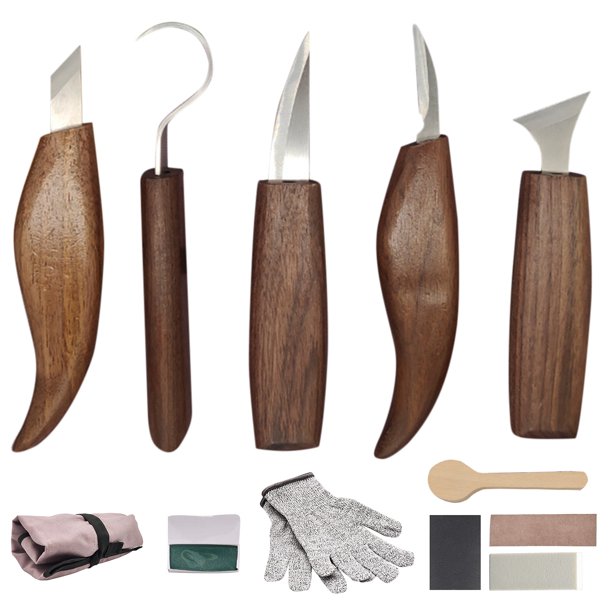
If chip carving has ever been something you've wanted to do, you know how difficult it can be. There are many different styles and techniques that you can try, but which one is best? What tools are necessary? I will be sharing my tips and tricks for carving chips. There are many essentials to chip carving success, regardless of whether you prefer traditional or modern style.
Traditional
Chip carving is one of the oldest forms of decorative woodcarving. A straight-edged knife is required, however, a skew ground or offset blade knife may also be used. Chip carving involves making numerous small triangular holes in the wood to create a pattern. This art form originated over 1,000 years ago. It was so popular that many designs looked the same across nations, making it difficult to tell which one was which.
The skills needed to carve wood became more popular as the practice spread around the globe. Chip carving was a popular way to decorate furniture in Sweden. Eventually, schools were opened to teach the craft. Modern chip carvers can benefit from centuries-old chip carvers' skills and knowledge. Through the generations, knowledge and experience was passed down from carver to apprentice and student. It's an ongoing process that lasts for a lifetime.
Free form
If you've always wanted to try chip carving, you've come to the right place. Murray Taylor's DVD shows you how to make freeform and geometric carvings. It is a wonderful introductory project, with lots of information. English and NTSC formats can be found. The DVD is also available in stereo and widescreen formats. Artisan Media Ltd. holds the DVD. It can also be downloaded in MP4 format to Windows and Mac computers.
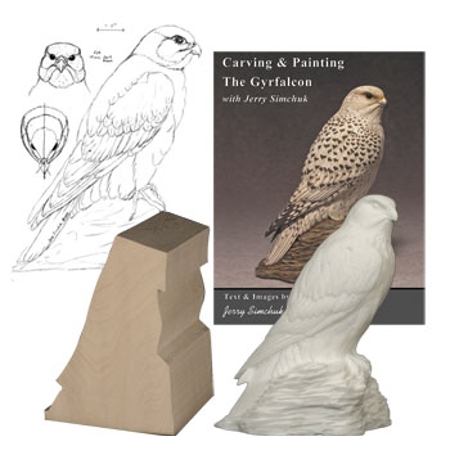
The basic shapes in geometric chip carving are triangles, circles, and lines. This technique allows for endless shapes and patterns, and can also be used to combine various styles. This method of chip carving is also called freeform chip carving. You can make your chips look beautiful in any room, no matter whether they are a flower, a dragon or a tree. You can incorporate multiple techniques into one piece by free-form chip carving.
Techniques
Chip carving is a tradition that has existed for many centuries. There are many examples all over the world. On paddles used for ceremonial purposes and boats in the South Pacific Islands, one example of chip-carving is found. Most likely, these carvings were made with pieces of bone and shells. However, some people report using shark teeth. This book shows you how to create beautiful designs with a variety of chip-carving techniques.
If you are able to follow some simple steps, chip carving can be easy. The first step is to learn how you can carve the fine triangle. This pattern is easy to understand and easy to execute. Simply carve several triangles and continue this process until you have carved the pattern. However, chip carving doesn't have be boring. Variation of the triangles can give you a wide variety of patterns.
Tools
Lora Irish offers an online seminar for free that will cover the basics of chip-carving. She teaches you how to use various carving tools and supplies, including a chip knife, stab knife, and detail bench knife. Irish also teaches you how to use different wood carving tools during this seminar. To find the right tool for you, choose from the following list. These tools are versatile enough to create simple shapes or intricate designs.
A chip carving knife uses special geometry. It measures about one and a half inches in length with a narrow, curving back edge. This allows for precise incisions. A sharp point is essential to ensure that edges meet perfectly. A sharp tip is also available for chip carving knives made of stainless-steel. A chip carving knife should be sharp and sharp enough to slice a bit of wood.
Getting started
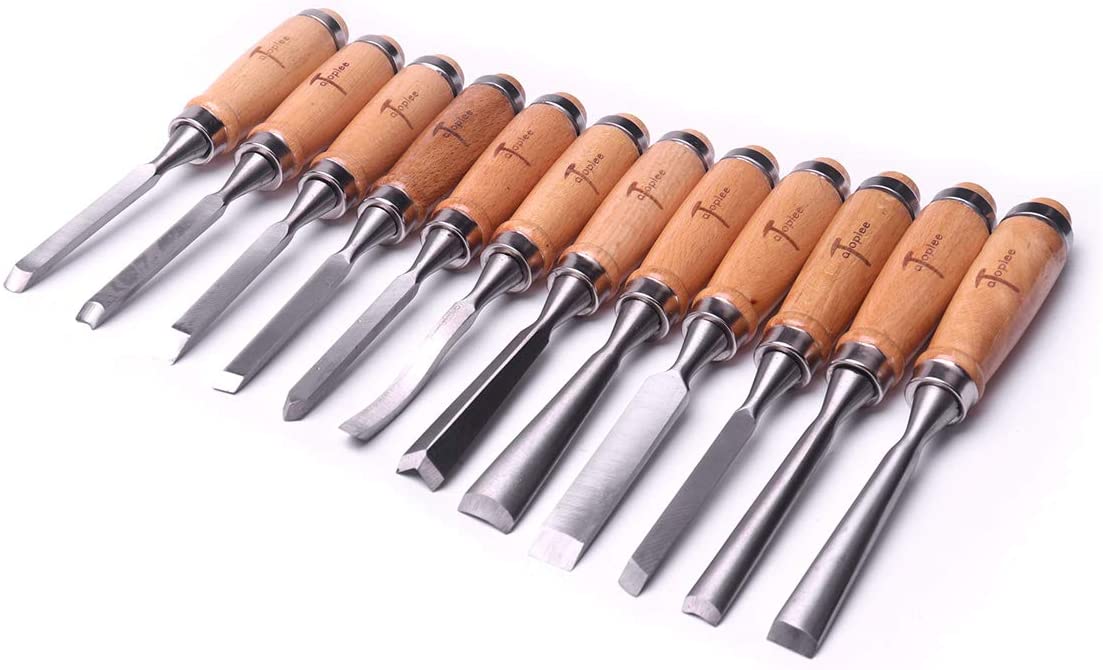
You must learn the basics of chip carving before you start. This process varies based on the type of carving that you intend to do. You should still be familiar with some principles in order to make sure your work is as precise as possible. Chip carving is a technique that involves creating a fine pattern in wood. Follow these steps to create your very first chip carve.
It is important to properly sharpen a chip carving knife. The blade of the chip carving knife will have bevels on each side, indicating that it is a primary chip carving knife. The sharpening stones are shaped like diamonds and can create efficient edges. Place it at a ten degree angle. The stone will both sharpen and shave the chip carving knives and tool simultaneously.
FAQ
How often should I get new supplies?
Over time, you may need to replace your tools. Hand tools will need to be sharpened regularly. For power tools, replacement parts will be required frequently. Try spreading your purchases over a few months so you don't buy too many at once.
What tools should I start with when becoming a woodworker?
Woodworking is an art. It requires patience. It takes time for you to master the different techniques and tools that are required to woodwork.
There are many types of woodworking equipment on the market today. Some prefer power tools while some prefer hand tools.
The choice is yours, but you must ensure you choose the right tool for the job. A basic set of hand tools may be enough for you if your skills are not yet developed.
Another option is to learn how to use a router, which is used for cutting intricate shapes into wood. You can find these at most hardware stores.
What is the difference in plywood and particleboard?
Plywood is made of layers of wood that are pressed together under pressure. Plywood is available in a variety of thicknesses. It is often used to make cabinets or flooring. Particle board is made up of sawdust mixed in resin, then compressed into large pieces. It is used primarily for home improvements. Both boards are strong and can be easily cut.
Which wooden items are very popular?
Wood that has been harvested sustainably is the best-selling type of wood.
Most furniture is made from oak, maple, mahogany or walnut.
These woods are strong and durable, with beautiful grain patterns. They can also last for years if they are properly cared for.
To protect wood furniture from moisture damage, it should be painted first. All surfaces should be painted, including doors, drawers, and handles.
A paint that resists water is the best choice to ensure that furniture lasts a long time.
It is recommended to use an oil-based primer, then apply two coats. Depending on how often it will be worn, you may need to apply several coats.
Avoid spray cans and aerosol paints. These products contain solvents which evaporate quickly and leave behind harmful fumes.
What kinds of woods are good for making furniture?
Woods are classified according their hardness. Softwoods include pine, fir, cedar, and cypress. They are great for outdoor furniture as they resist rot. These hardwoods include maple, mahogany and teak. Because they can't weather outside, they're usually used indoors.
How much money will I need to get started?
Because each project is unique there are no exact numbers. But if you want to get an idea of how much money you'll need, consider these factors:
-
Material cost
-
Tools and equipment
-
The time spent on the project
-
Hourly rate
-
How much profit can you anticipate to make
-
You can hire help, regardless of whether you have a plan.
It's a good idea for beginners to start with small projects like frames and boxes. As you gain experience, you'll be able to tackle more complex projects.
Statistics
- Overall employment of woodworkers is projected to grow 8 percent from 2020 to 2030, about as fast as the average for all occupations. (bls.gov)
- If your lumber isn't as dry as you would like when you purchase it (over 22% in Glen Huey's opinion…probably over 10-15% in my opinion), then it's a good idea to let it acclimate to your workshop for a couple of weeks. (woodandshop.com)
- The best-paid 10 percent make $76,000, while the lowest-paid 10 percent make $34,000. (zippia.com)
- Most woodworkers agree that lumber moisture needs to be under 10% for building furniture. (woodandshop.com)
External Links
How To
How to join wood with no nails
Woodworking is a hobby that many people enjoy doing. It's fun and relaxing because you can use your hands to make something useful from wood. Sometimes you may want to join two pieces together of wood without using nails. This article will show you how to do it to make your woodwork projects look great.
The first thing you'll need to do is cut off any rough edges from your pieces of wood before joining them together. Sharp corners can cause problems down the line. Now you can start gluing the boards together.
You should only glue one side of hardwood. For softwoods like cedar and pine, glue should be applied to both sides. After applying the glue, press the boards firmly until they are completely stuck together. Before you proceed to the next step, be sure to let the glue dry completely.
Once you've glued your boards together you will need to drill holes in the joints to accommodate screws. Depending on what type screw you choose, the size of these holes will depend on how big they are. If you are going to use a half-inch wood screw, you will need to drill at least 3/4 inch deep.
After drilling your holes, drive the screws into the board's backside. Avoid hitting the board's top surface. Otherwise, you could ruin the finish. Be careful not to drive the screws too hard at the ends. This will prevent the wood from splitting.
Protect your finished project now. You have two options: seal the whole furniture piece or just the top. Either way, you'll want to use a product that will last for years to come. You can choose from oil-based varnishes or polyurethane, shellac and lacquer as examples.
These products can usually be found at any home improvement store. It is important to ensure that you purchase the correct product for the job. Keep in mind that certain finishes can be toxic and should not be used indoors. Wear protective gear whenever you are handling them.