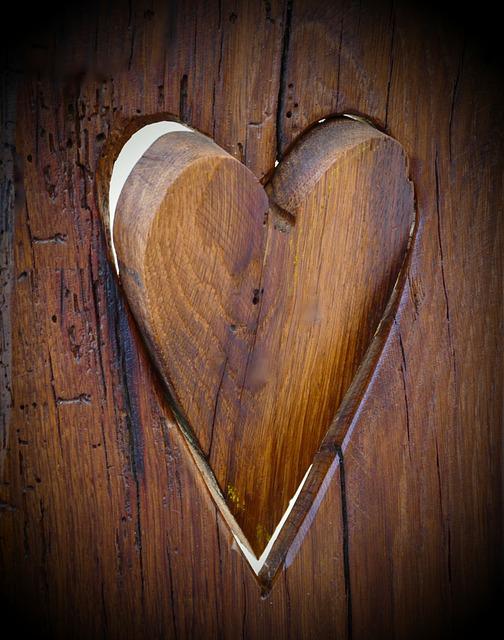
If you've ever wanted to try chip carving, then you've probably noticed that it can be a challenging task. There are many different techniques and styles you can try. But, which one is the best? What tools do I need? I will be sharing my tips and tricks for carving chips. There are many essentials to chip carving success, regardless of whether you prefer traditional or modern style.
Traditional
Chip carving is one the oldest forms decorative woodcarving. The knife must be straight-edged, but an offset or skew-ground knife can also work. Chip carving involves making numerous small triangular holes in the wood to create a pattern. This art form developed over 1,000 years ago. It has been adapted in many other countries. Due to its popularity, many of the designs were so similar across cultures that it was hard to distinguish one from the other.
As wood carving became more common, skills were passed on from generation to generation. Chip carving was used in Sweden to decorate furniture. Schools were eventually established to teach this art. The skills and knowledge of carvers from centuries ago have benefited modern chip carvers. Knowledge and experience were passed down through the generations from apprentice to student. It's a lifelong process that continues today.
Formulary free
If chip carving has been something you've wanted to try, this is the place for you. Murray Taylor has created a DVD that shows you how create both freeform and geometric carvings. It's a good introductory project and contains lots of useful information. NTSC and English formats are available. The DVD is also available in stereo and widescreen formats. The owner of the DVD is Artisan Media Ltd., and it is available in MP4 format for Windows and Mac computers.
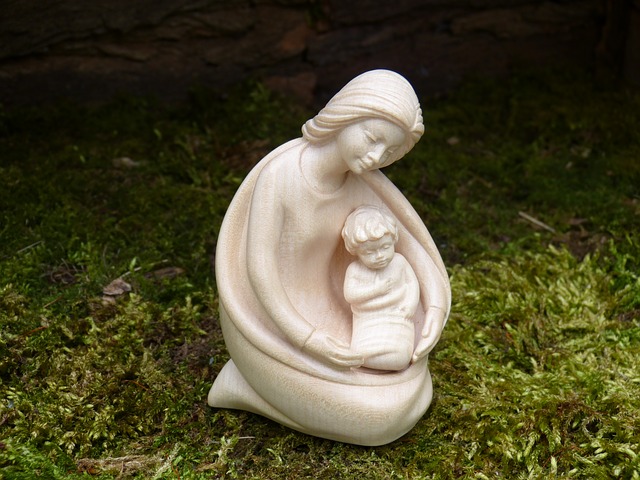
Triangles, circles and lines are the basic shapes of geometric chip carving. You can combine different styles with this technique, which allows you to create unlimited patterns and shapes. This method of chip carving is also called freeform chip carving. No matter what shape your chips are, they will add beauty to any room. It is possible to combine many techniques in one piece using free form chip carving.
Techniques
Chip carving has been around since the beginning of time. There are many examples all over the world. You can find chip carving on boats paddles and other ceremonial tools handles in the South Pacific Islands. Most likely, these carvings were made with pieces of bone and shells. However, some people report using shark teeth. This book demonstrates how to use a variety of chip carving techniques to produce stunning designs.
You can easily carve chip if your follow some basic steps. The first of these is to know how to carve the fine triangle. This pattern is easy to understand and easy to execute. This pattern is easy to carve. You simply need to cut various triangles, and then repeat the process. However, chip carving doesn't have be boring. Variation of the triangles can give you a wide variety of patterns.
Tools
Lora S. Irish offers a free online seminar that will teach you the basics of chip carving. She shows you how to use a variety of carving tools and materials, such as a chip, stab, and detail knife. Irish will also discuss the different types wood carving tools in this seminar. To find the right tool for you, choose from the following list. These tools are versatile enough to create simple shapes or intricate designs.
A chip carving knife uses special geometry. It measures approximately one-half inches in length and has a narrow, curved edge at the back. This allows you to make precise incisions. You should also choose a point that is sharp and needle-sharp so that the edges meet perfectly. Chip carving knives are also made of stainless steel and come with a sharp tip. A chip-carving knife should be sharp enough for cutting a small piece of wood.
Getting started
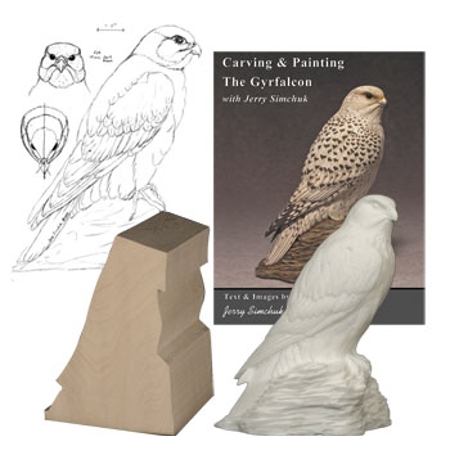
First, learn about chip carving. The process will vary depending on what type of carving you are doing. To ensure accuracy, it is important to be familiar with the following principles. Chip carving is a technique that involves creating a fine pattern in wood. These are the steps to create your first chip carving.
It is vital to sharpen your chip carving knife properly. Chip carving knives will have bevels along their blades, which indicates they are primary chip carving knives. The sharpening stone is shaped like a diamond and can produce efficient edges. Place it at a 10 degree angle. The stone will both sharpen and shave the chip carving knives and tool simultaneously.
FAQ
Can I make my living doing this job?
Yes! Many woodworkers are already doing so. According to the U.S. Bureau of Labor Statistics (BLS), the median annual wage for woodworkers was $34,000 in May 2012. This is significantly higher than the national average, which is $31,000 per year.
Are there any other things I should know regarding woodworking?
Furniture making is a laborious task. It's easy not to appreciate how hard it is. Finding the right wood is the hardest part. It can be hard to choose from the many types of wood that are available.
The problem with wood is that not all wood properties are the same. Some woods will warp over time, others will split or crack. You must take these things into consideration before purchasing wood.
How much does a hobbyist need to invest in getting started?
A lot of capital is required to purchase the necessary supplies and tools if you want to start your own woodworking shop. It's a good idea to buy a small tablesaw, drill press and circular saw. These items aren’t too expensive so you won’t have to break the bank.
Statistics
- Most woodworkers agree that lumber moisture needs to be under 10% for building furniture. (woodandshop.com)
- In 2014, there were just over 237,000 jobs for all woodworkers, with other wood product manufacturing employing 23 percent; wood kitchen cabinets and countertop manufacturing employing 21 percent. (theartcareerproject.com)
- If your lumber isn't as dry as you would like when you purchase it (over 22% in Glen Huey's opinion…probably over 10-15% in my opinion), then it's a good idea to let it acclimate to your workshop for a couple of weeks. (woodandshop.com)
- Average lumber prices rose about 600 percent between April 2020 and May 2021. (familyhandyman.com)
External Links
How To
Tips for driving a nail in wood
When driving a nail into wood, it is important to first choose the correct size and kind of hammer. Claw hammers include mallets, claw hammers (sledgehammers), mallets, ball-peen hammers, hatchets, and mallets. Each type of tool has its advantages and drawbacks. For example, a claw hammer works best when you want to hit something hard, like nails; however, it's difficult to control precisely where the blow lands. A sledgehammer is useful for striking large areas at once but too heavy to be effective for smaller tasks.
After selecting the right hammer, you will need to place your hand flat against one side of the head. The handle should rest comfortably in your hands. You can grip the handle with your fingers, but not so tight that it causes injury. The hammer should be held straight up with your wrist relaxed. Then swing the hammer back toward the ground, aiming for the center of the nail. The impact of the hammer hitting the nail should be felt. You can practice swinging the hammer with a block or wood until you feel the rhythm.
When you're ready to start driving the nail, hold the hammer in front of you close to your body. Place the nail so that it is perpendicular with the wood's surface. Keep your attention on the tip. Swing your hammer forward. Then follow through with the motions of the hammerhead. Continue this motion several times, slowly increasing the speed of each swing. Once you've mastered the technique, try adding power to your swings. To make it more powerful, hold the hammer up high to your shoulder and then bring it down. This will help you put more energy behind each of your moves.
Once you have successfully drilled the first hole in the nail, remove the hammer. Use a pry bar or screwdriver to pull out the rest of the nails. To prevent splitting the wood, ensure you keep the nail heads flush against the board's surface.