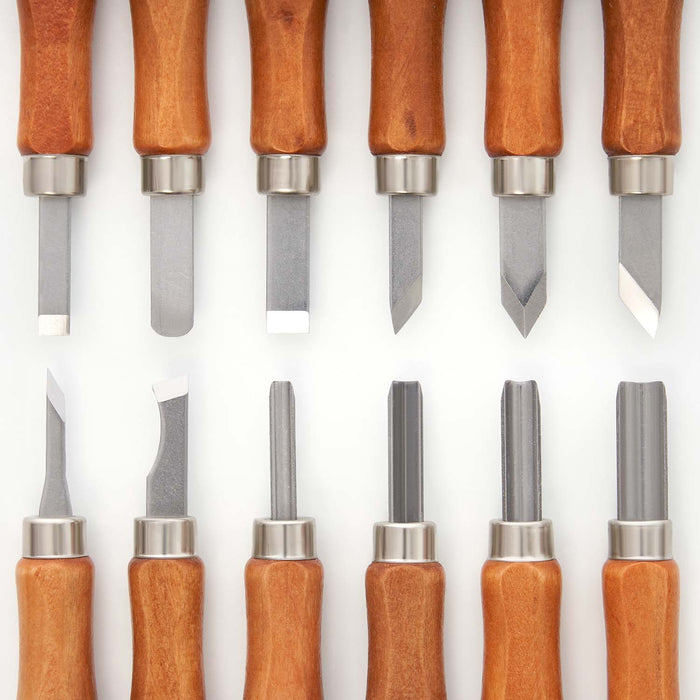
Many artists are starting to explore the art of wood carving with a chainsaw. The art is a natural extension their skill set. It often includes a combination traditional carving techniques and contemporary designs. Crager, along with Tracie Dugas his wife, have been carving beautiful wood creations together since the 1960s. Between shows, they often try to get home as many times as possible to help with staining and painting. His daughters are now involved in his work as well, helping out on occasion with painting or staining. They prefer to use white pine which is lighter and less likely than black pine to crack.
Rich Anderson
Rich Anderson is an Oregon chainsaw wood carver. He is a Poughkeepsie resident and lives in Oregon with his wife and their son. Anderson holds several degrees and teaches art in the Pre-K-5th grades. Anderson has carved many sculptures throughout Long Island. His sculptures range from tall trees to small pieces such as corn ear sculptures. He is currently working to create a sign for Youngs Farm, Riverhead.
A $400 chainsaw allows him to create beautiful sculptures that would take days to chisel out of a tree. Chainsaw wood carving can also be used to create beautiful sculptures that are more environmentally friendly than hammers and chisels. Anderson is a word-of mouth marketer and has carved a large cobra and a great Blue Heron for Wading Water's mechanic.
Tracie Dugas
Tracie Dugas created this life-sized wizard from wood. It is a stunning example of her skills as a chainsaw wood carver. The 49 year old young woman lives in Clare Nova Scotia, near Digby and Yarmouth. The chainsaw wood carver, was among many artists who showed their work during Canada Day weekend in Sydney. Although tourists flooded Sydney's waterfront, the dry spell allowed locals to take in the view of the chainsaw artist and enjoy the waterway.
Tim Crager
Tim Crager, while he didn't consider him an artist and wasn't very skilled with a saw chainsaw, turned his passion into a full time career in carving six years back. Crager has sold over $1 million in carvings throughout the Eastern U.S. Crager was raised in Garrett, Eastern Kentucky. His father was a chainsaw wood carver. Crager fell in love with the artist's art and gave his two-week notice to his boss.
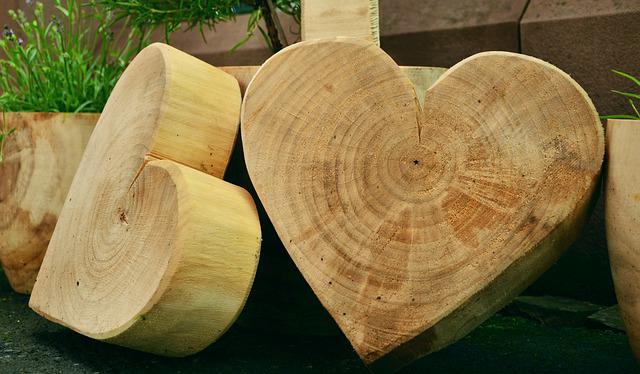
Crager prefers white pine when it comes to wood choice. It's readily available from tree trimming businesses. Many people prefer different types of wood. Crager follows the grain of the wood and lets the saw guide his creations. Crager may know exactly what he's making before he starts any project. However, he often changes his mind mid-project. A small project can be done in an hour, while a large one may take 33 to 35 hours.
Don Scoggins
Don Scoggins can be described as a chainsaw woodcarver. His wood carvings feature intricate details and many animals. His works have been admired by neighbors and tourists alike. Blue Arrow Farm's coffee shop and entrance are graced with the chainsaw sculptures. Blue Arrow Farm's owner is Don Oriolo. He also manages Felix the Cat. Don Oriolo and his wife, Kacie, met while competing in a chainsaw competition at the New Jersey State Fair.
The award-winning woodcarver started carving 15 years ago at a Reedsport, Oregon contest. He had already carved by hand, but he had never used a chainsaw before. His carvings now include an otter, a mother bear and a squirrel peeking out of a tree. And now, he's ready to compete at the National Chainsaw Carving Competition.
Dan Porter
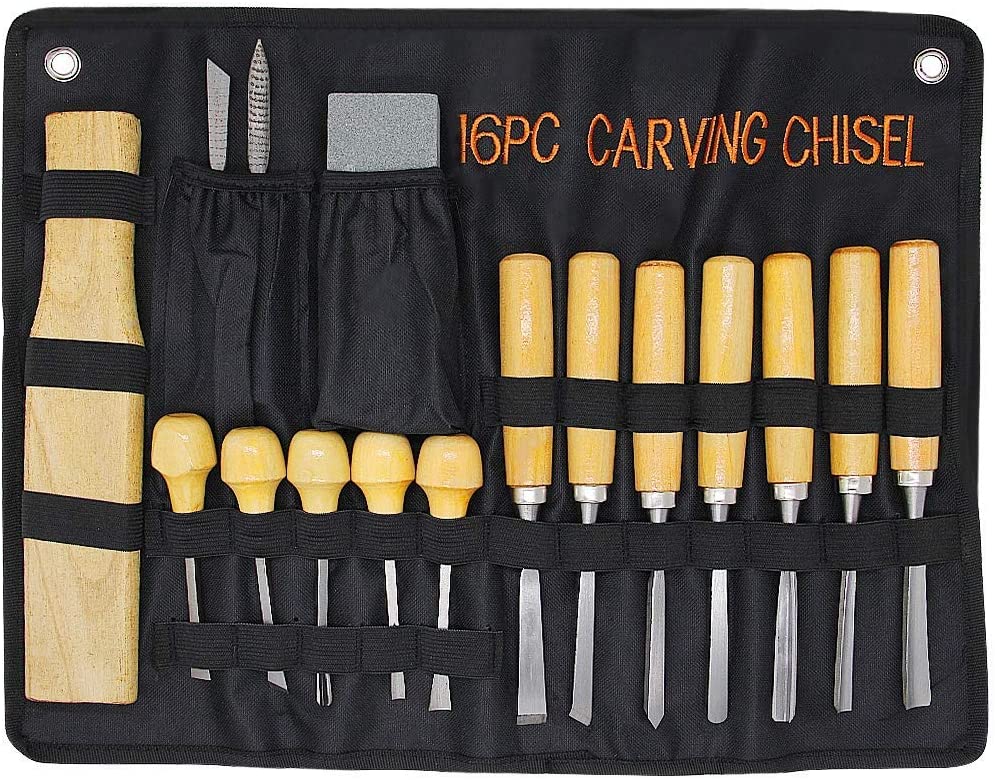
Dan Porter is a chainsaw wood carver and has been highly sought after for many years. His intricate and detailed carvings are admired worldwide. He was an accomplished wood carver who spent many years working in the lumber industry. These are some of his most notable achievements as a wood carver.
FAQ
How do you know which tools are the best for you?
It's important that you consider your needs and preferences while shopping for tools. Are you more comfortable with plastic or metal handles? What size of nails and screws do your hands use most? Are you more comfortable using power tools than hand tools?
What tools should you start with to become a woodworker
Woodworking is an art that takes patience and practice. It takes time for you to master the different techniques and tools that are required to woodwork.
There are many options for woodworking equipment today. Some people prefer to use power tools while others prefer manual tools.
You have the freedom to choose what tool you want, but it is important that you select the right tool for your job. It may be a good idea to start with a basic set, if possible, if you don’t know much about hand tools.
You could also try learning how to use a router which is used to cut intricate shapes into wood. These routers can be purchased at most hardware and home improvement stores.
Is it difficult to start my woodworking business?
It is difficult to start your own woodworking company. There are many regulations and legal requirements that you will need to comply with. This doesn't necessarily mean that you should go through all the work of setting up a company. Many people choose to join existing businesses. This allows you to join existing businesses and pay only membership fees.
Is it possible to learn woodworking by yourself?
You can learn everything best by doing. Woodworking is an intricate art form that requires practice, skill, patience, and experience. Any craft requires patience to master.
To actually learn something is the best way. Start small, and work your way up from there.
Is it necessary to be a genius in woodworking to succeed?
No. No. Woodworking isn't rocket science. You can create beautiful pieces of art by learning how to use simple power tools.
Statistics
- Most woodworkers agree that lumber moisture needs to be under 10% for building furniture. (woodandshop.com)
- The best-paid 10 percent make $76,000, while the lowest-paid 10 percent make $34,000. (zippia.com)
- Average lumber prices rose about 600 percent between April 2020 and May 2021. (familyhandyman.com)
- In 2014, there were just over 237,000 jobs for all woodworkers, with other wood product manufacturing employing 23 percent; wood kitchen cabinets and countertop manufacturing employing 21 percent. (theartcareerproject.com)
External Links
How To
How to join wooden boards without using nails
Many people love woodworking. Woodworking is a relaxing hobby that allows you to use your hands to create useful things from wood. However, there are times when you want to join two pieces of wood together without having to use nails. This article will help you to maintain the beauty of your woodwork projects.
First, remove any sharp edges from the wood pieces before you join them. Avoid leaving sharp edges that could lead to problems later. Now it's time to start glueing your boards together.
You should only glue one side of hardwood. You should glue both sides if you are working with softwoods such as pine and cedar. After applying the glue, press the boards firmly until they are completely stuck together. Make sure you let the glue dry before moving on to the next step.
After you've glued your boards, you'll want to drill holes into the joints where you plan to insert screws. Depending on what type screw you choose, the size of these holes will depend on how big they are. For example, if you're going to use a 1/2-inch wood screw, then you should drill a hole that is at least 3/4 inches deep.
After drilling your holes, drive the screws into the board's backside. Don't hit the board's surface. You could damage the finish. When driving the screws, try to avoid hitting the ends of the screws too much. This will prevent splitting the wood's end grain.
Now that your project is finished, you'll want to protect it from the elements. You can seal the furniture pieces or cover the top. You want it to last years, so you can use any product. Examples include oil-based varnishes and polyurethanes, shellac, lacquer and others.
These products can usually be found at any home improvement store. It is important to ensure that you purchase the correct product for the job. Remember that some finishes can be toxic, so you should not use them indoors. When handling certain finishes, wear protective gear.