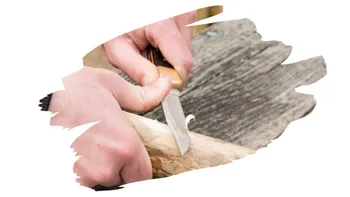
Woodcarving, or whittling, is one of two techniques. Both of these techniques involve removing wood from a larger piece of wood and changing it into a new shape. A spoon for the kitchen can be transformed into a carving measuring 10 feet. But the key difference is that both require you to take the wood material out of the original piece. Unlike whittling, which requires clamping, gluing, and joinery, wood carving does not involve any of those methods.
Woods that can be carved
There are many different types of wood that can be used to carve. There are many wood types that can be used for carving, including fresh, moist and rotten. The best ones are straight-grained and have minimal knots. This will help make carving easier. It is not recommended to carve wood with many knots or branches. For assistance in finding the right kind of wood, consult the park wardens or tree surgeons. They can point you in the right direction.
Pine is a great wood to carve. It is easy to find in the US. It is soft and contains knots, but it will hold its detail well. Pine will last a very long time if it is kept in good condition. In Norway, for example, the load-bearing orepine stave churches that have survived over eight hundred years have been preserved. This is a great choice if you're just starting out.
Useful tools
Before you can begin wood carving, draw your design on the wood. To cut straight lines, you can use your hand saw or a drill to make intricate details. Because it can remove large amounts of material quickly, the gouge is a great choice for rough shaping. It has an abrasive edge which makes it ideal for smoothing rough areas.
There are many kinds of knives. Bench knives, for example, can be used for finer detail. These can cut into wood and can also be used to remove larger parts in detail work. A chisel will be the best tool for cutting through thicker materials, but bench knives may also make delicate cuts. You can't go wrong with chip carving or whittling, but the right tools will make or break your project.
Techniques
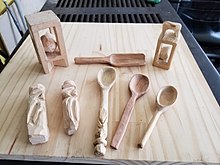
Sharp knives are necessary for precise, controlled cuts that are vital to good whittling or wood carving. A dull knife causes frustration, blisters, and tired hands. A sharp knife makes it easy to focus and more enjoyable. While carving, whittling enthusiasts can sit in deep thought and breathing rhythms, as they use the sharp blade to create intricate designs and details.
Like all crafts, there will be errors. However, this is all part of the process. Some of your first creations might be unsymmetrical or cut against the grain. Overly eager to carve your nose and end with no nose at all, you might be unable to control your impulses. You can learn from your mistakes and improve your skills. Wood carving is a satisfying hobby that can inspire others to try more complex designs.
Whittling is one of the most common wood-carving methods. This form of wood carving is the oldest and most popular. It uses either a pocketknife, or a straight knife. It is easier to carve softwoods than hardwoods. Whittling is characterized by knife marks. They don't need sanding or expensive tools.
Getting started

To get started in wood carving and whittling, you must first select a piece. Although you have the option to use many different wood types, beginners should start with basswood. Also, avoid wood with knots or holes. Carving smooth branches is much easier. You can buy beginner-level wooden items at craft stores. The following tips can help you get started with wood carving.
Use the correct tool. The whittling knife should be sharp and durable. You should use a quality blade for the first few cut. A sharp blade ensures better cuts. A dull blade will tend to glance at the wood and turn toward the hand. It can still cut human flesh. These tips should be followed when carving. It will simplify the whole process. Continue reading to learn about the art and craft of wood carving.
FAQ
Are there any other things I should know regarding woodworking?
It is easy to underestimate how much work it takes to make furniture. The hardest part of the process is actually finding the right wood. It can be hard to choose from the many types of wood that are available.
A problem is that wood doesn't have the same properties. Woods can warp, split, or crack over time. These are important considerations to make before you purchase wood.
What is the difference in a hobbyist and professional woodworker?
Hobbyists enjoy making things out of wood, whereas professionals focus more on the quality of their work. Hobbyists take great pride in their creations, and share them with family and friends. Before they start working on a project, professionals will spend hours researching the designs. They will pay attention to every detail, from selecting the best materials to finishing the project perfectly.
Are there any tips for starting a woodworking enterprise?
Starting a woodworking business is a lot of work. It's worth it if you're passionate and willing to work hard. You will probably love the challenge of starting your own business.
Remember that you may encounter unexpected problems when starting a new venture. Unexpectedly, money might run out. Or you might find that your customers aren’t willing or able to pay as much you had hoped. You need to be ready for these situations if you want to survive.
It is a good idea to create a separate bank account just for your company. This will ensure that you always know how much money has come in.
Statistics
- Average lumber prices rose about 600 percent between April 2020 and May 2021. (familyhandyman.com)
- Most woodworkers agree that lumber moisture needs to be under 10% for building furniture. (woodandshop.com)
- The U.S. Bureau of Labor Statistics (BLS) estimates that the number of jobs for woodworkers will decline by 4% between 2019 and 2029. (indeed.com)
- Overall employment of woodworkers is projected to grow 8 percent from 2020 to 2030, about as fast as the average for all occupations. (bls.gov)
External Links
How To
How to make wood joints
This tutorial will help you join two pieces of wooden together. We will use the pocket hole joint, which is drilling holes in the wood to join them. This method is great if your wood's straight and smooth. If your wood isn't straight or flat, you might want to try another method, such as dowel joinery. Here are the steps
-
Drill Pocket Hole Joints. Measure and mark the location where you would like to place the pocket hole joint. With a handheld drill machine or jig saw, drill 3/4-inch deep holes in the ends of each piece.
-
Sand Smooth. You can sand the edges of the wood to ensure that it doesn't split.
-
Glue Together Apply glue to both the ends of the wood. Let the wood sit for 5 minutes, then clamp it together.
-
Attach the Pieces together. After the glue has dried completely, you can clamp the pieces together until they are flush.
-
Trim Joinery. Trimming the joinery after glue has completely dried.
You should leave enough space between the pieces to allow you to turn them inside-out.